Cell Manufacturing Process
We manufacture high-efficiency solar cells.
Our consistent improvement in the technology and process, has made us achieve efficiencies over industry standards. Our metallization properties ensuring high aesthetic product value and ground breaking reliability of the product.
ISL cells also, have the unique distinction of exhibiting lower reverse current, a key metric of determining performance in low light conditions.
Solar Photovoltaic Cell Production Line
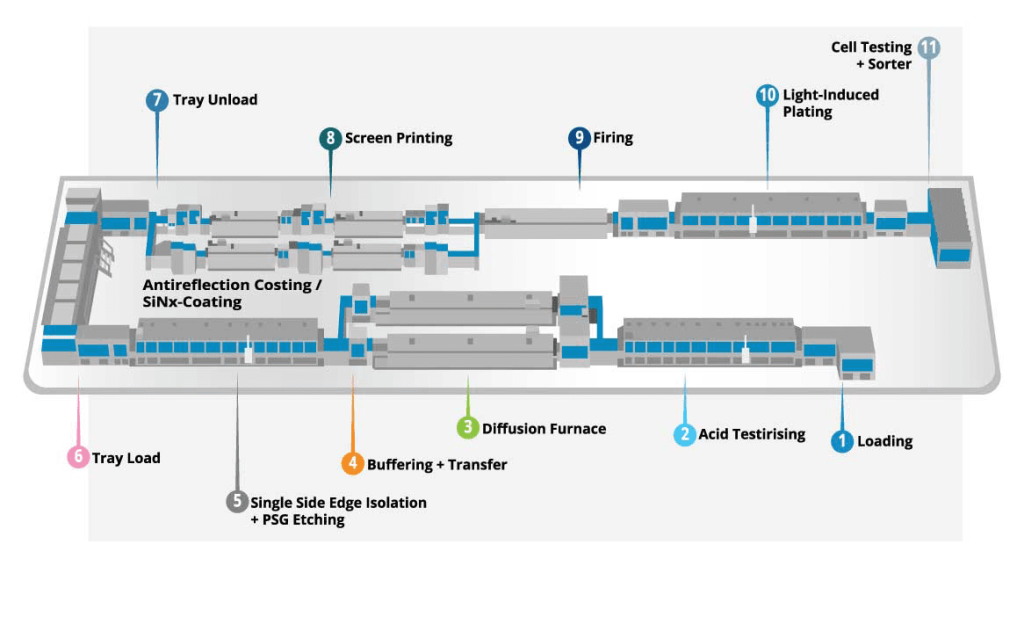
Cell Manufacturing Process
Automatic Loading Station
The wafers are loaded on the 1st machine which is the LCL in 5 trays of 100 pieces each. They then go through 2 camera’s, one which detects the geometry of the wafer and the other detects microcracks.
Diffusion Furnace
A common dopant source is POCl3. Other dopant deposition methods include screen printing, or chemical vapor deposition.
Cell Sorting
The cell sorter is the final machine in the cell manufacturing process, which sorts the cells in various categories like efficiency, colour, voltage/current into 48 different cases.
Acid Texturing
This process creates hills and valleys on the surface of the wafer so that the sunlight gets reflected rather than trapped. Wafers run through a cascading rinsing process starting with a KOH rinse followed by HF and HNO3. This process is known as ETCHING. The wafers are rinsed with DI (deionized water) which is the purest form of water, with the mobility of electrons.
PECVD - Plasma Enhanced Chemical Vapour Deposition
This machine provides the anti-reflective coating on the wafer so that there is a minimum reflection of the sunlight.
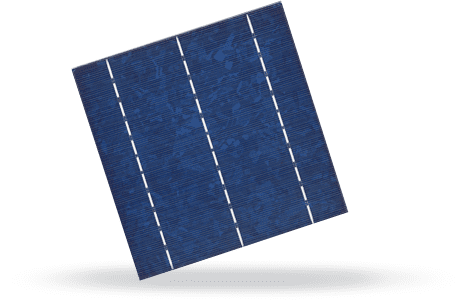
P-doping (Phosphorous Doping)
In this process, a layer of diluted phosphoric acid is applied on the wafer through the phosphorous mist. P doping is responsible to form the PN junction on the wafer.
Printing
After the PECVD in which the wafers acquire the blue colour. They go through the printing cycle. In the front and the back surface silver and aluminium paste are used to print the Bus bars, which help in the flow of electrons.
Module Manufacturing
Our modules are designed to the highest standards of quality, reliability and performance.
Our integrated manufacturing of cells and modules have been an imminent combination.
Our modules carry Industry leading 25-year power output warranty.
Fully Robotic Vertically Integrated Plant
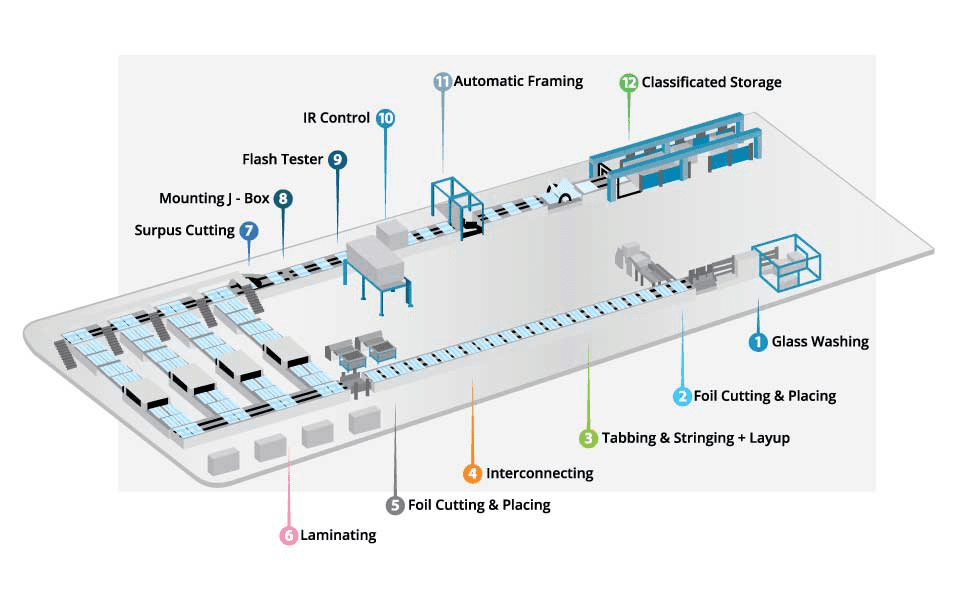
Module Manufacturing Process
Cell Tester
Here the cells are tested on different parameters like open circuit voltage, Short circuit current and Maximum power point curent and voltage respectively.
Electroluminescence Tester
This machine is able to detect micro-cracks/ degradation and shunt areas on the cell.
Sun Simulator
Is a device that provides natural sunlight. The machine is used for testing solar cells, sunscreen, plastic and other materials and devices under lab conditions.
Laser Cell Cutter
A laser cutter machine is used to cut cells according to the size of the module being produced.
PV Laminator
It is used to join all the layers forming the module, ensuring immunity to the cell against dust, moisture, humidity, and other environmental conditions.
Tabber & Stringer
This machine assembles and welds the photovoltaic cells together. Tabber connects ribbon on cells whereas the stringer connects one cell to another.
Framing & Sealing
The modules are finished with an aluminium frame around the edge. The frame increases mechanical strength, which makes it easier at the time of installation.
